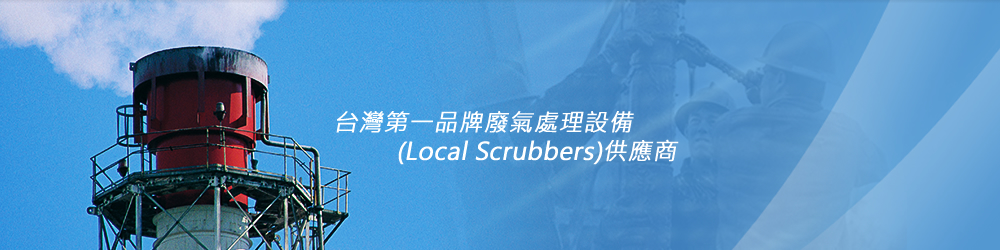

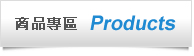
- + Wet-Thermal-wet
- + Plasma-Wet
- + Burn-wet
- + Thermal-Wet
- + Thermal-Dry(Catalyst)
- + Thermal- Dry -PCW
- + Burn-Dry
- + Wet-Burn-Wet
- + Dry Scrubber
- + Wet Thermal PFC Catalyst
- + PFC Catalyst
- + NH3 Catalyst(DeNOx)
- + 氨重組器 Ammonia Reformer
- + 餘氫發電
- + Wet Scrubber
- + Wet-EP
- + VOC Catalys
- + VOC Condenser
- + 緊急應變設備
- + N2防逆火
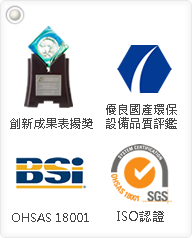
首頁>商品介紹>PFC Catalyst >PFC catalyst
PFC catalyst
1. Allows full decomposition of CF4, C2F6, C5F8 and other PFC
(perfluorocarbon), and SF6 and HFC. Eliminates the need for propane and
other combustion fuels for the heater heating system, thereby minimizing the
emissions of CO2.
2. Eliminates the need for any ancillary facility. Offers space-saving and
lower-cost features.
3. Ensures improved safety(flame and fuel are not necessary.)
4. Causes no NOx generation due to the relatively lower decomposition
temperature.
5. Requires no after-treatment equipment such as a wet scrubber since the
catalyst component is responsible for adsorption and fixation of fluorine.
Also keeps the system piping free from any possible corrosion.
催 化技術為PFC的防制提供低成本的方法,且不會對半導體製程造成衝擊。一般來說,當溫度到達約650 ~ 700°C的高溫時,在PFC內的C1到C4超過99%都會被破壞掉,而使用新型的PFC催化劑可在溫度較低時將PFC的NF3和SF6處理掉。此催化劑 相當穩定,即使延長使用期限仍能保持非常高的破壞效率。但SiF4的出現卻會對催化劑造成致命的破壞,因此在催化劑加入之前,必須先以刷洗系統過濾洗去 SiF4,以確保催化劑的使用效果。
PFC化合物是眾所周知一些氣體內主要的化學成份,例如像CF4與C2F6這些化合物,都是半導體元件在蝕 刻製程與反應腔清洗中非常重要的氣體。但PFC卻會對全球溫室效應產生重大的影響,使得半導體的製造過程均對它做嚴格的監控。雖然這類化合物僅佔全部輻射 的少部份,但它在大氣中卻可存在相當長的時間,因此累積起來就有很大的影響力。例如,CF4經預估在大氣中就有超過10000年的壽命。
PFC 化合物在半導體工業,常被選為晶片蝕刻與CVD反應室清洗的主要氣體。而現在反應室清洗製程所需的PFC催化破壞,已大大的減少,主要原因在於改用NF3 為主氣體,而NF3在電漿清洗製程中可被破壞達99%。儘管如此,最近卻有來自經濟上的分析,建議在效益上仍以氟碳化物來處理CVD的反應室並以催化法破 壞未使用的PFC。其主要的理由,包括:1) NF3的價格較C2F6與C3F8為高;2) NF3在全球市場的普及利用率;以及3) 形成中所需可觀的F2量與F2的純化過濾經濟成本。
催化劑常用來做為控制工業氟碳化物排放的方法。而整個催化的製程,是讓污物氣體通過催 化區,並透過適當的溫度提升,約略在150 ~ 400°C之間,即可讓揮發的有機化物 (VOC) 催化破壞。在經催化作用,這些有機物將成為CO2和H2O,同樣的,若原化合物有含鹵素元素,則將催化成一些礦物酸。雖然催化製程早已廣泛應用在VOC排 放的控制,但其技術卻是最近才被用來處理PFC排放的問題。此處是說明半導體製造如何利用催化破壞技術來處理PFC。
PFC的催化分解 催化劑在化學反應中所扮演的角色,其本身並非隨反應而耗損。而且,使用催化劑後,可以降低反應所需的最低溫度,如此可降低能量成本。降低污染的催化劑已 廣泛運用在揮發性有機污染物排放的控制。典型的空污破壞催化劑,內中常含一或數種活性高的催化金屬,(如鉑和鈀等),而由於這些催化金屬具有相當高的反應 速率,故也是常被選來做為處理此類反應的原因。
催化劑常被製成數種幾何形狀,包括細粒、串珠狀或是直接擠壓成型。有一種材料由於它內含多 條平行但不相通的方形通道,其形如蜂巢一般。因此,有時我們便直接稱它為「蜂巢」,而將催化劑直接鍍在這些通道上。有一種薄的催化劑,稱之為 「washcoat」,被鍍膜在這些通道的壁上,其內沉積了催化金屬。此種構造和其他形狀相比,多了一些優點,包括模組化設計、低壓降、極佳的催化金屬利 用率、可預測的流動特性、很好的質量與熱量傳遞特性、低熱質、以及低反應損失。也因為上述優點,故蜂巢狀已常被選擇做為主要構造。
催化劑被 選為降低應用的理由有下列數個,第一,由於催化劑能降低製程反應所需的溫度,通常只需攝氏數百度即可。如此一來,便可降低此應用所需操作溫度,進而也讓能 量成本減到最少。第二,因反應速率變快,故整個催化系統明顯小於相關的熱氧化系統。因此催化系統接觸反應所需時間僅約0.1 ~ 0.3秒,相較於熱氧化方式,則增加至1 ~ 2秒或更多。 而反應所需接觸時間縮短,換言之,其所需佔地面積更小,而須投資的成本也相對減少。第三,則是催化系統反應產物選擇性的優點。因為,越低的催化操作溫度, 可消除因氮原子養化所形成的Nox,如同其它氧化不完全的產物。
PFC化合物催化分解所需溫度仍低於所採用熱氧化的方法。舉例來說,若要 讓C2F6與C3F8採用熱分解法,則需超過1000°C以上的高溫,若是要分解CF4,則要高達2000°C才可進行熱分解。有趣的是,若採用催化劑分 解,則CF4會比C2F6、C3F8、c-C4F8更易被破壞分解。這樣的結果,幾乎與熱分解方式相反,而之所以存在這樣的差異,主要是由於反應機制不同 所造成。
用來分解C1-C4氟碳化物與CHF3的參與反應物,包括CO2和HF。由於反應完全,並沒有CO、Nox與半分解的化合物。至 於分解NF3的的催化反應物,則包括NOx與HF,有了選擇比100%的Nox,所有NF3內的氮原子均可轉換為Nox。另外,只要在製程氣體中加入少量 的氨化物,便可大量減少從NF3分解所排放出的Nox。至於分解SF6的催化反應物,則主要為Sox和HF。
PFC反應的催化作用為了能成功控制PFC的催化反應,即使延長使用期限,催化劑也要能維持相當好的分解效率 (例如,超過約一年的時間)。若希望能對大部份的PFC反應物達到高於95%的分解,則須在較高的操作溫度才行,由於在催化劑操作分解後期,會伴隨HF的產生。
在 空污分解應用所使用的催化劑,主要是白金的高活化金屬,並且散佈在氧化鋁的支撐材料上,但此催化劑卻有多個理由不適用於PFC的催化分解。雖然鉑群金屬為 高氧化性的催化劑,但會形成易揮發的鹵化物,如此內含的鹵元素便不能忍受超過400°C的操作溫度,雖然氧化鋁的熱穩定度超過800°C,但是卻會在與含 氟的化合物產生非揮發的固態AlF3。
如此一來,傳統的催化劑並不適用於PFC化合物的催化分解。而內含的基本金屬,雖不能如鉑群金屬 般反應,但卻不會在操作溫度升高時揮發。而非傳統的催化支撐物,主要為TiO2與ZrO2,因即使在含腐蝕的HF環境下,依然能保持其完整性,即使在較高 的操作溫度也相當穩定。由於這樣的特性,使其相當適於做為PFC的化合物分解。
(perfluorocarbon), and SF6 and HFC. Eliminates the need for propane and
other combustion fuels for the heater heating system, thereby minimizing the
emissions of CO2.
2. Eliminates the need for any ancillary facility. Offers space-saving and
lower-cost features.
3. Ensures improved safety(flame and fuel are not necessary.)
4. Causes no NOx generation due to the relatively lower decomposition
temperature.
5. Requires no after-treatment equipment such as a wet scrubber since the
catalyst component is responsible for adsorption and fixation of fluorine.
Also keeps the system piping free from any possible corrosion.
催 化技術為PFC的防制提供低成本的方法,且不會對半導體製程造成衝擊。一般來說,當溫度到達約650 ~ 700°C的高溫時,在PFC內的C1到C4超過99%都會被破壞掉,而使用新型的PFC催化劑可在溫度較低時將PFC的NF3和SF6處理掉。此催化劑 相當穩定,即使延長使用期限仍能保持非常高的破壞效率。但SiF4的出現卻會對催化劑造成致命的破壞,因此在催化劑加入之前,必須先以刷洗系統過濾洗去 SiF4,以確保催化劑的使用效果。
PFC化合物是眾所周知一些氣體內主要的化學成份,例如像CF4與C2F6這些化合物,都是半導體元件在蝕 刻製程與反應腔清洗中非常重要的氣體。但PFC卻會對全球溫室效應產生重大的影響,使得半導體的製造過程均對它做嚴格的監控。雖然這類化合物僅佔全部輻射 的少部份,但它在大氣中卻可存在相當長的時間,因此累積起來就有很大的影響力。例如,CF4經預估在大氣中就有超過10000年的壽命。
PFC 化合物在半導體工業,常被選為晶片蝕刻與CVD反應室清洗的主要氣體。而現在反應室清洗製程所需的PFC催化破壞,已大大的減少,主要原因在於改用NF3 為主氣體,而NF3在電漿清洗製程中可被破壞達99%。儘管如此,最近卻有來自經濟上的分析,建議在效益上仍以氟碳化物來處理CVD的反應室並以催化法破 壞未使用的PFC。其主要的理由,包括:1) NF3的價格較C2F6與C3F8為高;2) NF3在全球市場的普及利用率;以及3) 形成中所需可觀的F2量與F2的純化過濾經濟成本。
催化劑常用來做為控制工業氟碳化物排放的方法。而整個催化的製程,是讓污物氣體通過催 化區,並透過適當的溫度提升,約略在150 ~ 400°C之間,即可讓揮發的有機化物 (VOC) 催化破壞。在經催化作用,這些有機物將成為CO2和H2O,同樣的,若原化合物有含鹵素元素,則將催化成一些礦物酸。雖然催化製程早已廣泛應用在VOC排 放的控制,但其技術卻是最近才被用來處理PFC排放的問題。此處是說明半導體製造如何利用催化破壞技術來處理PFC。
PFC的催化分解 催化劑在化學反應中所扮演的角色,其本身並非隨反應而耗損。而且,使用催化劑後,可以降低反應所需的最低溫度,如此可降低能量成本。降低污染的催化劑已 廣泛運用在揮發性有機污染物排放的控制。典型的空污破壞催化劑,內中常含一或數種活性高的催化金屬,(如鉑和鈀等),而由於這些催化金屬具有相當高的反應 速率,故也是常被選來做為處理此類反應的原因。
催化劑常被製成數種幾何形狀,包括細粒、串珠狀或是直接擠壓成型。有一種材料由於它內含多 條平行但不相通的方形通道,其形如蜂巢一般。因此,有時我們便直接稱它為「蜂巢」,而將催化劑直接鍍在這些通道上。有一種薄的催化劑,稱之為 「washcoat」,被鍍膜在這些通道的壁上,其內沉積了催化金屬。此種構造和其他形狀相比,多了一些優點,包括模組化設計、低壓降、極佳的催化金屬利 用率、可預測的流動特性、很好的質量與熱量傳遞特性、低熱質、以及低反應損失。也因為上述優點,故蜂巢狀已常被選擇做為主要構造。
催化劑被 選為降低應用的理由有下列數個,第一,由於催化劑能降低製程反應所需的溫度,通常只需攝氏數百度即可。如此一來,便可降低此應用所需操作溫度,進而也讓能 量成本減到最少。第二,因反應速率變快,故整個催化系統明顯小於相關的熱氧化系統。因此催化系統接觸反應所需時間僅約0.1 ~ 0.3秒,相較於熱氧化方式,則增加至1 ~ 2秒或更多。 而反應所需接觸時間縮短,換言之,其所需佔地面積更小,而須投資的成本也相對減少。第三,則是催化系統反應產物選擇性的優點。因為,越低的催化操作溫度, 可消除因氮原子養化所形成的Nox,如同其它氧化不完全的產物。
PFC化合物催化分解所需溫度仍低於所採用熱氧化的方法。舉例來說,若要 讓C2F6與C3F8採用熱分解法,則需超過1000°C以上的高溫,若是要分解CF4,則要高達2000°C才可進行熱分解。有趣的是,若採用催化劑分 解,則CF4會比C2F6、C3F8、c-C4F8更易被破壞分解。這樣的結果,幾乎與熱分解方式相反,而之所以存在這樣的差異,主要是由於反應機制不同 所造成。
用來分解C1-C4氟碳化物與CHF3的參與反應物,包括CO2和HF。由於反應完全,並沒有CO、Nox與半分解的化合物。至 於分解NF3的的催化反應物,則包括NOx與HF,有了選擇比100%的Nox,所有NF3內的氮原子均可轉換為Nox。另外,只要在製程氣體中加入少量 的氨化物,便可大量減少從NF3分解所排放出的Nox。至於分解SF6的催化反應物,則主要為Sox和HF。
PFC反應的催化作用為了能成功控制PFC的催化反應,即使延長使用期限,催化劑也要能維持相當好的分解效率 (例如,超過約一年的時間)。若希望能對大部份的PFC反應物達到高於95%的分解,則須在較高的操作溫度才行,由於在催化劑操作分解後期,會伴隨HF的產生。
在 空污分解應用所使用的催化劑,主要是白金的高活化金屬,並且散佈在氧化鋁的支撐材料上,但此催化劑卻有多個理由不適用於PFC的催化分解。雖然鉑群金屬為 高氧化性的催化劑,但會形成易揮發的鹵化物,如此內含的鹵元素便不能忍受超過400°C的操作溫度,雖然氧化鋁的熱穩定度超過800°C,但是卻會在與含 氟的化合物產生非揮發的固態AlF3。
如此一來,傳統的催化劑並不適用於PFC化合物的催化分解。而內含的基本金屬,雖不能如鉑群金屬 般反應,但卻不會在操作溫度升高時揮發。而非傳統的催化支撐物,主要為TiO2與ZrO2,因即使在含腐蝕的HF環境下,依然能保持其完整性,即使在較高 的操作溫度也相當穩定。由於這樣的特性,使其相當適於做為PFC的化合物分解。