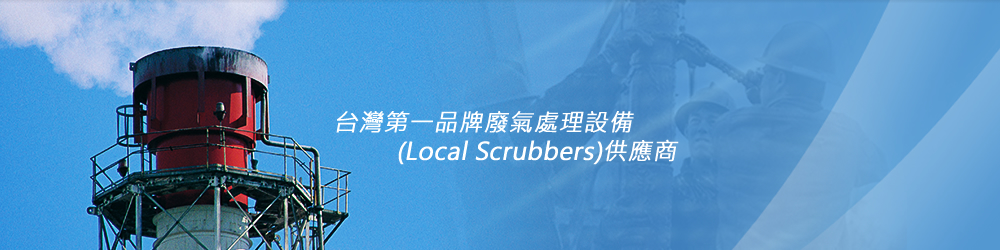

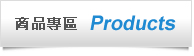
- + Wet-Thermal-wet
- + Plasma-Wet
- + Burn-wet
- + Thermal-Wet
- + Thermal-Dry(Catalyst)
- + Thermal- Dry -PCW
- + Burn-Dry
- + Wet-Burn-Wet
- + Dry Scrubber
- + Wet Thermal PFC Catalyst
- + PFC Catalyst
- + NH3 Catalyst(DeNOx)
- + 氨重組器 Ammonia Reformer
- + 餘氫發電
- + Wet Scrubber
- + Wet-EP
- + VOC Catalys
- + VOC Condenser
- + 緊急應變設備
- + N2防逆火
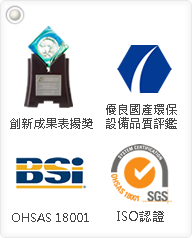
首頁>商品介紹>Burn-wet>ECS-3000(1500LPM)
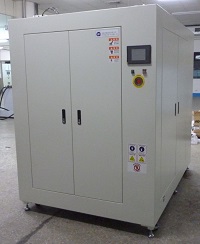
ECS-3000(1500LPM)
Model Name |
ECS-3000(1500LPM) |
Abatement Type |
Burn-Wet scrubbing |
Dimensions (mm) |
1200W x 1400D x 2000H |
Total Flow Rate |
1500 |
Working Temp |
1200ºC(Up to 1400ºC) |
Inlet ports |
NW-50 or ISO-80 |
Outlet port |
ISO-200 |
Application & DRE:
Target abatement gas
1. PFCs : NF3>99% , C2F6>95% , SF6>95% , CF4>90% , C3F8>95% , etc
2. Flammable gases : SiH4>99% , PH3>99%, TEOS>99%, H2>99% , AsH3 ,DCS, etc
3. Water soluble gases : Cl2 >99%,, HCl>99% , F2,HCl,HF, NH3, etc
4. Toxic gases: B2H6>99% WF6>99%
5.Others:TEPO>99% , C4F8>95%,TEB>99%,HBr >99%,SiCl4>99%, CH3F>99%
, CH2F2>99%, CHF3>99%, CH2F2>99%, SiH2Cl2、有機金屬、H2、CO、、N2O
、VOC 、GeH4 、SiF4 、 HMDSO
6.削減過程產生之生成NO2,NO,C2H4,CO副產物
Process:
Semiconductor,MOCVD,LCD,Solar
The abatement system is highly efficient, used in CVD and etch applications
for photovoltaic, semiconductor,TFT-LCD and other toxic,flammable gas
related industries.
Thin Film、Etching 、Diffusion
CVD process:SiH4,NH3,WF6,NF3,TEOS,TEOB ,etc
Diffusion Process:SiH4,NH3,PH3,DCS,ClF3,etc
Etch process:CxFy,SF6,CHxFy,HBr,etc.
The Burn-Wet Scrubber is designed for treating waste gas with fluorine
content. Combining high-temperature combustive decomposition and
hydro dissolution, the process waste gas reacts into a powder or dissolves
in the water by way of two-stage high-temperature combustion in the
reaction chamber; it is then dis...ged into the disposal facilities of the
plan via another water trough. The system is capable of handling special
gases used by most semiconductor and TFT-LCD manufacturers. The
maintenance frequency is low and the maintenance time is short,
minimizing the impact to the production schedule.燃燒水洗式廢氣處理機是一個專門處理含氟性氣體的廢氣處理系統,它混合了高溫
燃燒分解及水溶解的過程,將製程所產生的廢氣,經由反應室二階段的高溫燃燒,
反應成粉末,或是反應成溶解於水中的物質,再經由另一道程序的水槽而排放至廠
務處理系統,所處理的廢氣,包含大部份半導體廠及TFT - LCD 廠所使用的特殊氣
體,維修保養的頻率少且時間短,不會影響生產的時程。
The ECS-3000 series point-of-use abatement systems are highly efficient systems used in CVD- and etching applications for photovoltaic, semiconductor and other related industries. New process tools and technologies with highly corrosive gases and increasing gas loads are introduced.
The ECS-3000 series enjoys all the advantages such as high cleaning efficiency for PVCs and other gases, reliable abatement of all waste gases from CVD and etching processes, ...ion of various fuel gases and is in compliance with all international safety standards.
The system is designed for maximum corrosion resistance and to handle large amounts of solid reaction by-products.
Advantages:
As new process tools and technologies with highly corrosive gases and increasing gas loads are introduced, further improvements in abatement technologies are needed. The Burn-Wet scrubber meets those requirements and is in compliance with international safety standards.
Burn-Wet provides a couple of advantages such as a high destruction removal efficiency for all waste gases from CVD and etching processes, especially for PFCs as well as all kinds of solid and gaseous reaction by-products.
Burn-wet was designed for a reliable, resource- conserving performance even under harsh process conditions. The separation of the functional units such as burner, combustion chamber, wet scrubber, waste gas inlet and cooling system allows a flexible setup for each application.
A hardware interlock system equipped with sensors that constantly monitor all combustion/scrubbing factors such as chamber pressure, fuel gas, scrubbing water, temperature, etc. is provided to ensure stable and safe operation of the equipment. Excellent safety interlocks including flow, temperature, pressure, and leak sensors.
Graphic touch panel enables easy ...ion of operating conditions. Also, a user-friendly interface is provided for monitoring the equipment status. Software is available for a central control network system that enables multiple equipment monitoring and control from one location.
The footprint of the equipment is the smallest of all combustion type scrubbing equipment.
Hazardous substances of process waste gases are abated directly from where they originate (Point-of-Use). Waste gases are fed into a ring-shaped burner apparatus where thermolysis sets in. Depending on the chemical composition of the waste gases, various reactions take place (oxidation, reduction, pyrolysis). In the subsequent scrubbing process, gaseous and solid compounds generated by combustion are absorbed and cooled down by a suitable scrubbing liquid.
Top-down burner design minimizes clogging of burner nozzles
Monitoring interface for Ethernet or RS485
Wide range of fuel gases like liquefied natural gas city gas, coal gas, hydrogen, propane, butane, etc.
Double pressure gauge for monitoring inlet pressure and outlet pressure.
Double chamber design with independent control systems for automatic by pass. (Option)
As an alternative to the scrubber liquid’s through-feed-system the reactor can be equipped with a water-conserving closed-loop design. The reactors are available in any sizes, and runs with all fuel gases and scrubber liquids.
The machine uses circulating water mostly, water consumption is fairly low.
The separation of the functional units such as burner, combustion chamber, wet scrubber, waste gas inlet and cooling system allows a flexible setup for each application.
The customized abatement configuration is key to keep the maintenance interval as long as possible and to maximize the uptime.
High process flow capacity (100~3000LPM) up to 6-inlet for multiple process tools connection and total backup function to reduce total CoO
High thermal capacity (200~600LPM H2) for Epi & WCVD
Low CoO (O2 not required) with “On-demand” process mode utilities reduction(Option)
High reliability with “No flame out” technology
All IPI systems have a small footprint with service and maintenance access from the front and back. Installation is quick and easy and does not require specialized equipment.
The following equipment options are available for all IPI systems:
Fuel Gas: NG, LPG, H2
Oxidant: O2, CDA
Heated feed lines and inlets
Process-Tool-Interface
Signal Tower
Drip Pan
Earthquake Safety Kit
IPI Burn-Wet was specifically developed for applications involving large amounts of hydrogen as they typically occur in epitaxy processes. The system runs on various fuel gases, meets the highest safety standards, and is equipped with a water feed-through-system, which enables the dis...ge of large amounts of water without a cooling system.
IPI Burn-Wet 3000 DUO is a double-reactor offering two scrubbing systems that can operate simultaneously. It is optimized for up to four independent inlets of semiconductor and photovoltaic process tools. In case of malfunction or maintenance on one reactor, the other backs up the treatment of all waste gases (internal back-up), which ensures the equipment’s near 100 % uptime. Features:
Up to 2 independent waste gas and backup lines per reactor
Near 100 % operation time through backup function
Second reactor allows uninterrupted operation during maintenance
Runs with different fuel gases
Low water consumption through closed-loop design
IPI Burn-Wet TWIN – maximum Waste Gas Treatment due to Backup-Reactor
Maximum Waste Gas Treatment with IPI Burn-Twin
The customized abatement configuration is key to keep the maintenance interval as long as possible and to maximize the uptime.
Monitored emergency bypass dilution (Option)
Jet burner using fuel:Thermal oxidation
NOx reduction technology
Top down gas flow structure: minimizing powder build up
Simple maintenance through monitoring system
Global environmental regulations concerning PFC gases are becoming more and more stringent. It is a unique abatement system equipped with a burner that guarantees reliable PFC abatement to an unprecedented low level.
The system is equipped with a large water tank for efficient absorption of water soluble gases and solid burn products. The total waste capacity is 100 LPM~3000LPM including nitrogen purge from vacuum pumps.
IPI's burner-washers technology offers the greatest flexibility for exhaust gas abatement for the effluent gases used in Semiconductor, Photovoltaic - Solar, Thin Film, Compound Semiconductor manufacturing industries. It is designed for the abatement of both CVD and etch gases.
Highest standards of safety to eliminate any risks for operators and environment.
Lowest Cost of Ownership through low utility costs and by long maintenance intervals.
No risk of corrosion - Pipes are coated inside with corrosion resistant material.
The system operates with city water, no water pre-conditioning is required.
Integrating a multistage wet scrubber ensures a complete gas abatement of
the water reactive, water soluble and particulate formed after the combustion
stage.
The equipment is ready to operate immediately after the burners are fired on receiving an input command signal from the control panel and needs no pre/standby burning by the combustion reactor. In addition, a unique combustion algorithm is used to maintain fuel gas at the optimum quantity for each type of gas to be treated. Therefore, fuel gas consumption can be reduced.
A hardware interlock system equipped with sensors that constantly monitor all combustion/scrubbing factors such as chamber pressure, fuel gas, scrubbing water, temperature, etc. is provided to ensure stable and safe operation of the equipment. Excellent safety interlocks including flow, temperature, pressure, and leak sensors.
Graphic touch panel enables easy ...ion of operating conditions. Also, a user-friendly interface is provided for monitoring the equipment status. Software is available for a central control network system that enables multiple equipment monitoring and control from one location.
The footprint of the equipment is the smallest of all combustion type scrubbing equipment.
Hazardous substances of process waste gases are abated directly from where they originate (Point-of-Use). Waste gases are fed into a ring-shaped burner apparatus where thermolysis sets in. Depending on the chemical composition of the waste gases, various reactions take place (oxidation, reduction, pyrolysis). In the subsequent scrubbing process, gaseous and solid compounds generated by combustion are absorbed and cooled down by a suitable scrubbing liquid.
Top-down burner design minimizes clogging of burner nozzles
Monitoring interface for Ethernet or RS485
Wide range of fuel gases like liquefied natural gas city gas, coal gas, hydrogen, propane, butane, etc.
Double pressure gauge for monitoring inlet pressure and outlet pressure.
Double chamber design with independent control systems for automatic by pass. (Option)
As an alternative to the scrubber liquid’s through-feed-system the reactor can be equipped with a water-conserving closed-loop design. The reactors are available in any sizes, and runs with all fuel gases and scrubber liquids.
The machine uses circulating water mostly, water consumption is fairly low.
The separation of the functional units such as burner, combustion chamber, wet scrubber, waste gas inlet and cooling system allows a flexible setup for each application.
The customized abatement configuration is key to keep the maintenance interval as long as possible and to maximize the uptime.
High process flow capacity (100~3000LPM) up to 6-inlet for multiple process tools connection and total backup function to reduce total CoO
High thermal capacity (200~600LPM H2) for Epi & WCVD
Low CoO (O2 not required) with “On-demand” process mode utilities reduction(Option)
High reliability with “No flame out” technology
All IPI systems have a small footprint with service and maintenance access from the front and back. Installation is quick and easy and does not require specialized equipment.
The following equipment options are available for all IPI systems:
Fuel Gas: NG, LPG, H2
Oxidant: O2, CDA
Heated feed lines and inlets
Process-Tool-Interface
Signal Tower
Drip Pan
Earthquake Safety Kit
IPI Burn-Wet was specifically developed for applications involving large amounts of hydrogen as they typically occur in epitaxy processes. The system runs on various fuel gases, meets the highest safety standards, and is equipped with a water feed-through-system, which enables the dis...ge of large amounts of water without a cooling system.
IPI Burn-Wet 3000 DUO is a double-reactor offering two scrubbing systems that can operate simultaneously. It is optimized for up to four independent inlets of semiconductor and photovoltaic process tools. In case of malfunction or maintenance on one reactor, the other backs up the treatment of all waste gases (internal back-up), which ensures the equipment’s near 100 % uptime. Features:
Up to 2 independent waste gas and backup lines per reactor
Near 100 % operation time through backup function
Second reactor allows uninterrupted operation during maintenance
Runs with different fuel gases
Low water consumption through closed-loop design
IPI Burn-Wet TWIN – maximum Waste Gas Treatment due to Backup-Reactor
Maximum Waste Gas Treatment with IPI Burn-Twin
Access to maintenance area on front and back side
IPI Burn-Wet TWICE - Dual Waste Gas Treatment is a double-system with two independent burn/wet systems with a common control and media supply. It is optimized for up to eight independent inlets of semiconductor and photovoltaic process tools. Different fuel gases and washing liquids can be used. Access for operation and maintenance is found at the front and back. Operation costs and general safety can be optimized with a process tool interface.
IPI Burn-Wet: Gas Decomposition by Combustion) is a high efficient universal abatement system for abatement of the waste gases in the semiconductor, solar and thin films manufacturing. It is designed for the abatement of both CVD and etch gases. Global environmental regulations concerning PFC gases are becoming more and more stringent. The IPI Burn-Wet is a unique abatement system equipped with a patented "rolling" burner that guarantees reliable PFC abatement to an unprecedented low level. The system is equipped with a large water tank for efficient absorption of water soluble gases and solid burn products. The total waste capacity is 100~3000 LPM including nitrogen purge from vacuum pumps.
IPI Burn-Wet is specifically designed to meet the requirements of processes in photovoltaic Si-thin film manufacturing and is capable of treating larger amounts of hydrogen and NF3 (or F2).
Burn-Wet使用廢氣減排系統是應用於半導體,光電以及其它相關產業的化學氣相沉積和蝕刻等領域的一種高性能系統.
Burn-Wet滿足這些要求,並符合國際安全標準。此外,它提供了許多優點,如自CVD和蝕刻製程的所有廢氣高破壞去除效率,特別是對全氟化合物,以及各種固體和氣體反應的副產物。
該系統的設計,即使在惡劣的製程條件下是極可靠的,即使在嚴苛的製程條件下仍具有節約性能
延長維護周期和最大化正常運轉時間的秘訣是為客戶量身定制的廢氣減排系統,廢氣總流量100LPM~3000LPM
可高效處理沉積與蝕刻氣體
監控的緊急Bypass稀釋(Option)
更大的反應腔體容量,以提供更佳的處理效率
結合燃燒式及濕式系統:100LPM~6000LPM.
高分解效率
固定的火燄長度,長期穩定性運作
多種安全性感應器,以提供操作上之安全環境
具有危害自動停機,以防止不正確操作導致之危險發生
最適合於可燃性,活性,非活性氣體的處理
可以同時處理製程氣體及潔淨氣體
可以高效分解,處理包括PFCs氣體在內的地球溫暖化氣體
運行成本低(針對處理對象氣體,可以調節燃料供給量)
燃燒水洗式廢氣處理機是一個專門處理含氟性氣體的廢氣處理系統,它混合了高溫燃燒分解及水溶解的過程,將製程所產生的廢氣,經由反應室二階段的高溫燃燒,反應成粉末,或是反應成溶解於水中的物質,再經由另一道程序的水槽而排放至廠務處理系統,所處理的廢氣,包含大部份半導體廠及TFT - LCD 廠所使用的特殊氣體,維修保養的頻率少且時間短,不會影響生產的時程。
可依製程提供2~8個廢氣處理入口端。
處理量可到達 100LPM~6000LPM 。
工作溫度高達 1200~1400 度,有效處理PFC Gas。
中央端監控系統,隨時掌握機台狀況。
機台多使用循環水,用水量相當節省。
DP Senser:雙壓力計,監測進口壓力與出口壓力。
LCD 觸控式螢幕,具中文或英文介面,人性化操作。
高去除效率(DRE )
低運轉成本,根據製程來控制燃燒火頭性能
改良的耐腐蝕反應腔體上蓋
自上向下燃燒器的設計, 降低燃燒火頭噴嘴的堵塞
燃料氣的選擇性高,如液化天然氣,城市煤氣,煤氣,氫氣,丙烷,丁烷等
雙腔體各自獨力的控制系統,可設計自動By-Pass。
反應腔體有特殊防阻塞、 抗腐蝕之設計,能延長機台 PM 週期,縮短 PM 時間。
電路人機介面 PLC 控制系統,穩定及準確,維修亦簡單迅速。
具 SEMI 認證, interlock 、即時警報、故障排除…等安全機制。
獨立燃燒方式,完全燃燒之火焰渦流可燃性毒性氣體從低濃度至100%濃度均可用高溫處理
保養簡單保養可在極短的時間內完成,費用也低廉。
高信賴性構造簡單且零件數少,值得高度信賴。
選購配備:出口端風車、CMS中央監控系統、By-Pass自動切換系統 、加熱槍及加熱帶、水質酸鹼測量供應系統
處理流量(Total flow rate) 100~6000LPM is available for customized design.
Target abatement gas
1. PFCs : NF3>99% , C2F6>95% , SF6>95% , CF4>90% , C3F8>95% , etc
2. Flammable gases : SiH4>99% , PH3>99%, TEOS>99%, H2>99% , AsH3 ,DCS, etc
3. Water soluble gases : Cl2 >99%,, HCl>99% , F2,HCl,HF, NH3, etc
4. Toxic gases: B2H6>99% WF6>99%
5.Others:TEPO>99% , C4F8>95%,TEB>99%,HBr >99%,SiCl4>99%, CH3F>99%
, CH2F2>99%, CHF3>99%, CH2F2>99%, SiH2Cl2、有機金屬、H2、CO、、N2O
、VOC 、GeH4 、SiF4 、 HMDSO
6.削減過程產生之生成NO2,NO,C2H4,CO副產物
Process:
Semiconductor,MOCVD,LCD,Solar
The abatement system is highly efficient, used in CVD and etch applications
for photovoltaic, semiconductor,TFT-LCD and other toxic,flammable gas
related industries.
Thin Film、Etching 、Diffusion
CVD process:SiH4,NH3,WF6,NF3,TEOS,TEOB ,etc
Diffusion Process:SiH4,NH3,PH3,DCS,ClF3,etc
Etch process:CxFy,SF6,CHxFy,HBr,etc.
The Burn-Wet Scrubber is designed for treating waste gas with fluorine
content. Combining high-temperature combustive decomposition and
hydro dissolution, the process waste gas reacts into a powder or dissolves
in the water by way of two-stage high-temperature combustion in the
reaction chamber; it is then dis...ged into the disposal facilities of the
plan via another water trough. The system is capable of handling special
gases used by most semiconductor and TFT-LCD manufacturers. The
maintenance frequency is low and the maintenance time is short,
minimizing the impact to the production schedule.燃燒水洗式廢氣處理機是一個專門處理含氟性氣體的廢氣處理系統,它混合了高溫
燃燒分解及水溶解的過程,將製程所產生的廢氣,經由反應室二階段的高溫燃燒,
反應成粉末,或是反應成溶解於水中的物質,再經由另一道程序的水槽而排放至廠
務處理系統,所處理的廢氣,包含大部份半導體廠及TFT - LCD 廠所使用的特殊氣
體,維修保養的頻率少且時間短,不會影響生產的時程。
The ECS-3000 series point-of-use abatement systems are highly efficient systems used in CVD- and etching applications for photovoltaic, semiconductor and other related industries. New process tools and technologies with highly corrosive gases and increasing gas loads are introduced.
The ECS-3000 series enjoys all the advantages such as high cleaning efficiency for PVCs and other gases, reliable abatement of all waste gases from CVD and etching processes, ...ion of various fuel gases and is in compliance with all international safety standards.
The system is designed for maximum corrosion resistance and to handle large amounts of solid reaction by-products.
Advantages:
As new process tools and technologies with highly corrosive gases and increasing gas loads are introduced, further improvements in abatement technologies are needed. The Burn-Wet scrubber meets those requirements and is in compliance with international safety standards.
Burn-Wet provides a couple of advantages such as a high destruction removal efficiency for all waste gases from CVD and etching processes, especially for PFCs as well as all kinds of solid and gaseous reaction by-products.
Burn-wet was designed for a reliable, resource- conserving performance even under harsh process conditions. The separation of the functional units such as burner, combustion chamber, wet scrubber, waste gas inlet and cooling system allows a flexible setup for each application.
A hardware interlock system equipped with sensors that constantly monitor all combustion/scrubbing factors such as chamber pressure, fuel gas, scrubbing water, temperature, etc. is provided to ensure stable and safe operation of the equipment. Excellent safety interlocks including flow, temperature, pressure, and leak sensors.
Graphic touch panel enables easy ...ion of operating conditions. Also, a user-friendly interface is provided for monitoring the equipment status. Software is available for a central control network system that enables multiple equipment monitoring and control from one location.
The footprint of the equipment is the smallest of all combustion type scrubbing equipment.
Hazardous substances of process waste gases are abated directly from where they originate (Point-of-Use). Waste gases are fed into a ring-shaped burner apparatus where thermolysis sets in. Depending on the chemical composition of the waste gases, various reactions take place (oxidation, reduction, pyrolysis). In the subsequent scrubbing process, gaseous and solid compounds generated by combustion are absorbed and cooled down by a suitable scrubbing liquid.
Top-down burner design minimizes clogging of burner nozzles
Monitoring interface for Ethernet or RS485
Wide range of fuel gases like liquefied natural gas city gas, coal gas, hydrogen, propane, butane, etc.
Double pressure gauge for monitoring inlet pressure and outlet pressure.
Double chamber design with independent control systems for automatic by pass. (Option)
As an alternative to the scrubber liquid’s through-feed-system the reactor can be equipped with a water-conserving closed-loop design. The reactors are available in any sizes, and runs with all fuel gases and scrubber liquids.
The machine uses circulating water mostly, water consumption is fairly low.
The separation of the functional units such as burner, combustion chamber, wet scrubber, waste gas inlet and cooling system allows a flexible setup for each application.
The customized abatement configuration is key to keep the maintenance interval as long as possible and to maximize the uptime.
High process flow capacity (100~3000LPM) up to 6-inlet for multiple process tools connection and total backup function to reduce total CoO
High thermal capacity (200~600LPM H2) for Epi & WCVD
Low CoO (O2 not required) with “On-demand” process mode utilities reduction(Option)
High reliability with “No flame out” technology
All IPI systems have a small footprint with service and maintenance access from the front and back. Installation is quick and easy and does not require specialized equipment.
The following equipment options are available for all IPI systems:
Fuel Gas: NG, LPG, H2
Oxidant: O2, CDA
Heated feed lines and inlets
Process-Tool-Interface
Signal Tower
Drip Pan
Earthquake Safety Kit
IPI Burn-Wet was specifically developed for applications involving large amounts of hydrogen as they typically occur in epitaxy processes. The system runs on various fuel gases, meets the highest safety standards, and is equipped with a water feed-through-system, which enables the dis...ge of large amounts of water without a cooling system.
IPI Burn-Wet 3000 DUO is a double-reactor offering two scrubbing systems that can operate simultaneously. It is optimized for up to four independent inlets of semiconductor and photovoltaic process tools. In case of malfunction or maintenance on one reactor, the other backs up the treatment of all waste gases (internal back-up), which ensures the equipment’s near 100 % uptime. Features:
Up to 2 independent waste gas and backup lines per reactor
Near 100 % operation time through backup function
Second reactor allows uninterrupted operation during maintenance
Runs with different fuel gases
Low water consumption through closed-loop design
IPI Burn-Wet TWIN – maximum Waste Gas Treatment due to Backup-Reactor
Maximum Waste Gas Treatment with IPI Burn-Twin
The customized abatement configuration is key to keep the maintenance interval as long as possible and to maximize the uptime.
Monitored emergency bypass dilution (Option)
Jet burner using fuel:Thermal oxidation
NOx reduction technology
Top down gas flow structure: minimizing powder build up
Simple maintenance through monitoring system
Global environmental regulations concerning PFC gases are becoming more and more stringent. It is a unique abatement system equipped with a burner that guarantees reliable PFC abatement to an unprecedented low level.
The system is equipped with a large water tank for efficient absorption of water soluble gases and solid burn products. The total waste capacity is 100 LPM~3000LPM including nitrogen purge from vacuum pumps.
IPI's burner-washers technology offers the greatest flexibility for exhaust gas abatement for the effluent gases used in Semiconductor, Photovoltaic - Solar, Thin Film, Compound Semiconductor manufacturing industries. It is designed for the abatement of both CVD and etch gases.
Highest standards of safety to eliminate any risks for operators and environment.
Lowest Cost of Ownership through low utility costs and by long maintenance intervals.
No risk of corrosion - Pipes are coated inside with corrosion resistant material.
The system operates with city water, no water pre-conditioning is required.
Integrating a multistage wet scrubber ensures a complete gas abatement of
the water reactive, water soluble and particulate formed after the combustion
stage.
The equipment is ready to operate immediately after the burners are fired on receiving an input command signal from the control panel and needs no pre/standby burning by the combustion reactor. In addition, a unique combustion algorithm is used to maintain fuel gas at the optimum quantity for each type of gas to be treated. Therefore, fuel gas consumption can be reduced.
A hardware interlock system equipped with sensors that constantly monitor all combustion/scrubbing factors such as chamber pressure, fuel gas, scrubbing water, temperature, etc. is provided to ensure stable and safe operation of the equipment. Excellent safety interlocks including flow, temperature, pressure, and leak sensors.
Graphic touch panel enables easy ...ion of operating conditions. Also, a user-friendly interface is provided for monitoring the equipment status. Software is available for a central control network system that enables multiple equipment monitoring and control from one location.
The footprint of the equipment is the smallest of all combustion type scrubbing equipment.
Hazardous substances of process waste gases are abated directly from where they originate (Point-of-Use). Waste gases are fed into a ring-shaped burner apparatus where thermolysis sets in. Depending on the chemical composition of the waste gases, various reactions take place (oxidation, reduction, pyrolysis). In the subsequent scrubbing process, gaseous and solid compounds generated by combustion are absorbed and cooled down by a suitable scrubbing liquid.
Top-down burner design minimizes clogging of burner nozzles
Monitoring interface for Ethernet or RS485
Wide range of fuel gases like liquefied natural gas city gas, coal gas, hydrogen, propane, butane, etc.
Double pressure gauge for monitoring inlet pressure and outlet pressure.
Double chamber design with independent control systems for automatic by pass. (Option)
As an alternative to the scrubber liquid’s through-feed-system the reactor can be equipped with a water-conserving closed-loop design. The reactors are available in any sizes, and runs with all fuel gases and scrubber liquids.
The machine uses circulating water mostly, water consumption is fairly low.
The separation of the functional units such as burner, combustion chamber, wet scrubber, waste gas inlet and cooling system allows a flexible setup for each application.
The customized abatement configuration is key to keep the maintenance interval as long as possible and to maximize the uptime.
High process flow capacity (100~3000LPM) up to 6-inlet for multiple process tools connection and total backup function to reduce total CoO
High thermal capacity (200~600LPM H2) for Epi & WCVD
Low CoO (O2 not required) with “On-demand” process mode utilities reduction(Option)
High reliability with “No flame out” technology
All IPI systems have a small footprint with service and maintenance access from the front and back. Installation is quick and easy and does not require specialized equipment.
The following equipment options are available for all IPI systems:
Fuel Gas: NG, LPG, H2
Oxidant: O2, CDA
Heated feed lines and inlets
Process-Tool-Interface
Signal Tower
Drip Pan
Earthquake Safety Kit
IPI Burn-Wet was specifically developed for applications involving large amounts of hydrogen as they typically occur in epitaxy processes. The system runs on various fuel gases, meets the highest safety standards, and is equipped with a water feed-through-system, which enables the dis...ge of large amounts of water without a cooling system.
IPI Burn-Wet 3000 DUO is a double-reactor offering two scrubbing systems that can operate simultaneously. It is optimized for up to four independent inlets of semiconductor and photovoltaic process tools. In case of malfunction or maintenance on one reactor, the other backs up the treatment of all waste gases (internal back-up), which ensures the equipment’s near 100 % uptime. Features:
Up to 2 independent waste gas and backup lines per reactor
Near 100 % operation time through backup function
Second reactor allows uninterrupted operation during maintenance
Runs with different fuel gases
Low water consumption through closed-loop design
IPI Burn-Wet TWIN – maximum Waste Gas Treatment due to Backup-Reactor
Maximum Waste Gas Treatment with IPI Burn-Twin
Access to maintenance area on front and back side
IPI Burn-Wet TWICE - Dual Waste Gas Treatment is a double-system with two independent burn/wet systems with a common control and media supply. It is optimized for up to eight independent inlets of semiconductor and photovoltaic process tools. Different fuel gases and washing liquids can be used. Access for operation and maintenance is found at the front and back. Operation costs and general safety can be optimized with a process tool interface.
IPI Burn-Wet: Gas Decomposition by Combustion) is a high efficient universal abatement system for abatement of the waste gases in the semiconductor, solar and thin films manufacturing. It is designed for the abatement of both CVD and etch gases. Global environmental regulations concerning PFC gases are becoming more and more stringent. The IPI Burn-Wet is a unique abatement system equipped with a patented "rolling" burner that guarantees reliable PFC abatement to an unprecedented low level. The system is equipped with a large water tank for efficient absorption of water soluble gases and solid burn products. The total waste capacity is 100~3000 LPM including nitrogen purge from vacuum pumps.
IPI Burn-Wet is specifically designed to meet the requirements of processes in photovoltaic Si-thin film manufacturing and is capable of treating larger amounts of hydrogen and NF3 (or F2).
Burn-Wet使用廢氣減排系統是應用於半導體,光電以及其它相關產業的化學氣相沉積和蝕刻等領域的一種高性能系統.
Burn-Wet滿足這些要求,並符合國際安全標準。此外,它提供了許多優點,如自CVD和蝕刻製程的所有廢氣高破壞去除效率,特別是對全氟化合物,以及各種固體和氣體反應的副產物。
該系統的設計,即使在惡劣的製程條件下是極可靠的,即使在嚴苛的製程條件下仍具有節約性能
延長維護周期和最大化正常運轉時間的秘訣是為客戶量身定制的廢氣減排系統,廢氣總流量100LPM~3000LPM
可高效處理沉積與蝕刻氣體
監控的緊急Bypass稀釋(Option)
更大的反應腔體容量,以提供更佳的處理效率
結合燃燒式及濕式系統:100LPM~6000LPM.
高分解效率
固定的火燄長度,長期穩定性運作
多種安全性感應器,以提供操作上之安全環境
具有危害自動停機,以防止不正確操作導致之危險發生
最適合於可燃性,活性,非活性氣體的處理
可以同時處理製程氣體及潔淨氣體
可以高效分解,處理包括PFCs氣體在內的地球溫暖化氣體
運行成本低(針對處理對象氣體,可以調節燃料供給量)
燃燒水洗式廢氣處理機是一個專門處理含氟性氣體的廢氣處理系統,它混合了高溫燃燒分解及水溶解的過程,將製程所產生的廢氣,經由反應室二階段的高溫燃燒,反應成粉末,或是反應成溶解於水中的物質,再經由另一道程序的水槽而排放至廠務處理系統,所處理的廢氣,包含大部份半導體廠及TFT - LCD 廠所使用的特殊氣體,維修保養的頻率少且時間短,不會影響生產的時程。
可依製程提供2~8個廢氣處理入口端。
處理量可到達 100LPM~6000LPM 。
工作溫度高達 1200~1400 度,有效處理PFC Gas。
中央端監控系統,隨時掌握機台狀況。
機台多使用循環水,用水量相當節省。
DP Senser:雙壓力計,監測進口壓力與出口壓力。
LCD 觸控式螢幕,具中文或英文介面,人性化操作。
高去除效率(DRE )
低運轉成本,根據製程來控制燃燒火頭性能
改良的耐腐蝕反應腔體上蓋
自上向下燃燒器的設計, 降低燃燒火頭噴嘴的堵塞
燃料氣的選擇性高,如液化天然氣,城市煤氣,煤氣,氫氣,丙烷,丁烷等
雙腔體各自獨力的控制系統,可設計自動By-Pass。
反應腔體有特殊防阻塞、 抗腐蝕之設計,能延長機台 PM 週期,縮短 PM 時間。
電路人機介面 PLC 控制系統,穩定及準確,維修亦簡單迅速。
具 SEMI 認證, interlock 、即時警報、故障排除…等安全機制。
獨立燃燒方式,完全燃燒之火焰渦流可燃性毒性氣體從低濃度至100%濃度均可用高溫處理
保養簡單保養可在極短的時間內完成,費用也低廉。
高信賴性構造簡單且零件數少,值得高度信賴。
選購配備:出口端風車、CMS中央監控系統、By-Pass自動切換系統 、加熱槍及加熱帶、水質酸鹼測量供應系統
處理流量(Total flow rate) 100~6000LPM is available for customized design.