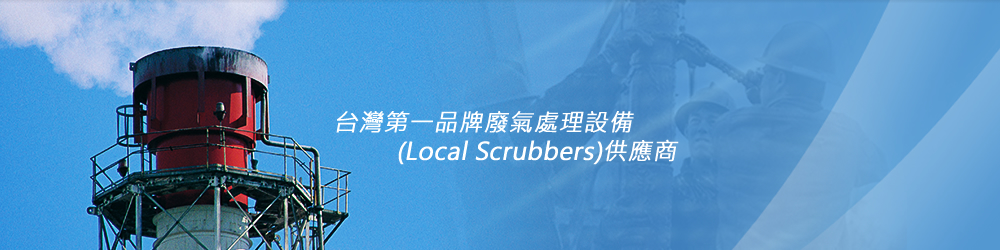

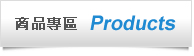
- + Wet-Thermal-wet
- + Plasma-Wet
- + Burn-wet
- + Thermal-Wet
- + Thermal-Dry(Catalyst)
- + Thermal- Dry -PCW
- + Burn-Dry
- + Wet-Burn-Wet
- + Dry Scrubber
- + Wet Thermal PFC Catalyst
- + PFC Catalyst
- + NH3 Catalyst(DeNOx)
- + 氨重組器 Ammonia Reformer
- + 餘氫發電
- + Wet Scrubber
- + Wet-EP
- + VOC Catalys
- + VOC Condenser
- + 緊急應變設備
- + N2防逆火
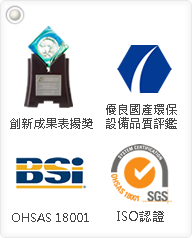
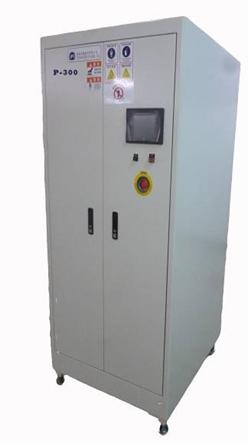
Scrubber Model |
P-300A(X) |
Abatement Type |
Plasma-Wet |
Total Flow Rate |
600LPM~1000LPM
|
Working Temp |
1400℃(Max up to 10000 ℃ ) |
Inlet ports |
NW50 / ISO80 (UP To 4/6) |
Outlet port |
ISO 100 / ISO160 |
Dimensions |
1000mmW * 1100mmD * 1900mmH |
Target abatement gas
PFC gases : NF3, SF6, C2F6, C3F8,C4F8,WF6,CHF3 etc.for chamber cleaning process.
Flammable gases : SiH4, DCS, TEOS, H2, PH3 etc.
Water soluble gases : BCl3, Cl2, HF, HCl, NH3 etc.
Others:N2O ,CFC-12海龍,R-12,戴奧辛etc.
Application Processes:
本機型適用於半導體產業及光電產業
P-300A treat flammable,toxic and global warming gases coming from semiconductor manufacturing processes.Especially it can treat PFCs perfectly using generated thermal plasma arc with high temperature around 1400 degree C by electrical power and nitrogen.
Solar 、 Thin Film、Etching 、Diffusion(For Semiconductor LCD panel industries)
Waste gas abatement in processes such as dry-etch, LP, and PE-CVD;abatement of PFC gases such as C4F8,NF3 and SF6 .
Toxic,Flammable Gas for CVD process.
Etching:CxFy,CHxFy(CHF3),NF3,SF6,HBr,SiCl4,Cl2,BCl3 etc
PECVD:DEPO(SiH4,SiH4,TEOS,NH3,N2O)Cleaning(NF3,C2F6,C3F8)
LPCVD:SiCl4,SiH2Cl2,Si2Cl6,TiCl4
MOCVD:Metal Organic compound
CVD:SiH4,NF3,WF6,B2H6,C3H6,TEOS,TMP,TMB ,C2F6,C3F8,C3H6,NH3,SiCl4,SiH2Cl2,Si2Cl6,TiCl4,Metal Organic compound etc.
Diffusion Process:SiH4,NH3,PH3,DCS,ClF3,F2.NF3 etc.
Metal(Al,Ti,Mo,W) Etching(BCl3,SF6)
SiO2>95%
Wetch back:SF6
Bosch Process:C4F8+SF6
Si2H6
Advantage:
1. High active thermal arc plasma flame.
2. High abatement efficiency for PFC gases(99%).
3. Plasma burner design (patent) provides a stable supply of plasma.
4. Excellent safety interlock system
5. Excellent durability and corrosion resistance structure
7. Relatively lower utility and operation cost(Longer torch life time and longer PM term than other competitors)
8. Simple operation and simple structure for easy maintenance.
9. SEMI-S2 certificated
10.Removal of nano-particles
11.To solve the problem of white smoke
12.Vertical structure : Strong for powder clogging13. Abatement system for persistent PFC gas using atmospheric plasma
14.Due to a stable high temperature from the direct current plasma, it can decompose and purify persistent PFC gas like SF6 and, etc.
15.Decomposes simultaneously.It is possible to handle PFC gas like NF3 and SF6 and halogen like HBr simultaneously.
16.No unnecessary fossil fuels.No unnecessary initial cost of construction of fossil fuel pipe and running cost of fossil fuel.
17.Using direct current atmospheric plasma.Security from accidental fires due to stable dis...ges and protected electricity.
18.Simple structure of torch and reactor. Due to simple structure of reactor tank plasma generating portion, it realizes easy-maintenance and low-cost.
19.Scrubber system operate safely and completely abate oxidized gas including power .
20.Original abatement for gas including power
21.The driving force for the development was to reduce the emission of PFC's (C2F6, C3F8, etc.) as perfluorinated carbons are contributing to the global warming process because of their extremely long atmospheric lifetimes even in small mass emissions.
22.Due to the fact that neither burn gases nor high electrical power is needed for operation the cost of ownership is minimized compared to existing concepts.
23.The basic concept of the Atmospheric Plasma Scrubber is the decomposition of PFC's and their reaction products in the remote plasma followed immediately by a wet scrubbing stage.
24.There is no formation of undesired compounds after the plasma treatment, no risk of HF formation inside the vacuum pump, no corrosion risk and no risk of particulate back-diffusion into the process chamber.
25.Only electrical power required, no other energy sources necessary
26.High energy density
27.Adjustable/tunable to the process needs
28.Low operational risk compared to other thermal systems
29.This system uses thermal plasma technology as its core technology. Thermal plasma abatement process can be used to destroy any liquid or gaseous organic waste. The correct application of low cost "front-end" or pre-preparation technologies in combination with this system can provide a very cost competitive solution independent of the level of contamination. The process is ideally suited to the destruction of concentrated forms of halogenated organic waste.
30.Space-saving design for installation space
31.The thermal plasma abatement process can be used in many industries and for many applications, some of which follow:
A.For the destruction of special wastes such as ozone depleting substances i.e. Halons (fire extinguishing compounds), Perfluorocarbons (PFC) and Chlorofluorocarbons (CFC's)
B.For the destruction of any of the controlled substances outlined in the Montreal Protocol, annexes A, B and C.
C..As a superior and cost effective alternative to incineration for the destruction of the "dirty dozen" persistent organic pollutants (POPS): Dioxins, Furans, Aldrin, Chlordane, DDT, Dieldrin, Endrin, Heptachlor, Hexachlorobenzene (HCB), Mirex and Toxaphene, Polychlorinated Biphenyl (PCB)
D.As an integral component for in-situ waste management (cleaner production) in the chemical and pharmaceutical industries
E.The destruction of chemical warfare agents
F.As a relocatable destruction process suitable for on-site remediation and small scale applications
32.Benefits of the Thermal Plasma in Abatement Application:
A.Ultimate elimination of hazardous waste either ‘in-process’ or stockpiled.
B."In-process" applications offer significant potential to boost productivity and product quality, i.e. the introduction of beneficial processes that might otherwise produce hazardous by-products is now possible
C.It offers extremely safe operation. The entire process is fully computer controlled and monitored, and only a small volume of waste is processed at any given time
D.No toxic residues are generated
E.Emissions to the atmosphere are substantially lower than existing and proposed international standards. International Toxic (dioxin) Equivalent emissions (I-TEQ) <0.1ng/m3
F.Operators can be readily trained to operate the system. G.High reliability.
H.Prevent waste gas re-combination solution.
G.PH auto control(Option)
H.Plasma torch current real time monitor and alarm.
I.The Plasma is compatible with PFC gases such SF6 that are difficult to abate with existing waste gas abatement systems. This state-of-the-art system minimizes running costs while maximizing abatement throughput.
J..No harmful vapors are emitted.
K.No odors are associated with the process
L.Relative to comparable destruction technologies the capital cost is low.
M.Servicing is simple, clean and inexpensive.
N.Compact ,smallfoot print
O.Easy Installation:No special facility request Power/Water/N2/CDA
P.Easy Maintenance:Chamber cool down and heat up to working temp in 30min.
33.Option for NaOH version on special application
34.P-300A is an equipment which completely decomposes flammable,corrosive,toxic and PFC gases through the plasma which is ignited by electricity and Torch.
35.10000 ~14000degree C of Arc zone.
36.P-300A destroies inflammable,corrosive and hazardous PFC gases by breaking them down into radicals or ions by plasma and passing them through a specially designed water spray zone.
37.P-300A also copes with powder such as SiO2 through and through a perfect interlock system,safety is secured and utility consumption is minimized.
38.Solution for abatement of PFC gases,such as C2F6,NF3,SF6 and CHF3
Plasma-wet Abatement system for persistent PFC gas using atmospheric plasma Due to a stable high temperature from the direct current plasma, it can decompose and purify persistent PFC gas like SF6 etc..
No unnecessary fossil fuels.No unnecessary initial cost of construction of fossil fuel pipe and running cost of fossil fuel.
Using direct current atmospheric plasma.Security from accidental fires due to stable dis...ges and protected electricity.
Simple structure of reactor.Due to simple structure of reactor tank plasma generating portion, it realizes easy-maintenance and low-cost
39.Corrosion-resistant technology and material
40.Anti accumulation system inside the wet tank.Special structure to prevent powder accumulating.
41.Reducing water usage with the water circulation system
42. P-300A treat flammable, toxic and global warming gases coming from semiconductor manufacturing process. Especially it can treat PFCs perfectly using generated thermal plasma arc with high temperature by electrical power and nitrogen.
43.Low cost of ownership.
44.Pyrolysis using heat source 10000~14000 degree C of electric arc dis...ge.
45.NOx free system.
46.Top down gas flow structure minimizing powder build up
47.Simple maintenance through monitoring system
48.High quality and ultimate safety.
49.High decomposition efficiency in treating PFCs gases.
50.Automatic anti-clogging pressure control in scrubber(PLC Control)
51.Preventing CO2 generation(No need of fuel gas)
52.Perfect decomposition of toxic gases in high-temperature thermal Plasma
53.Pressure Control:Measure the accurate pressure and powder clogging through PID-type pressure.
54.Auto Control System:
PLC based touch screen display
Auto/Manual modes&easy control
Fast-responding&highly accurate PLC Control
Operability:
Simple maintenance through monitoring system.
Minimizing maintenance time
By-pass system…Maximizing the operating ratio of main tool.
Technologies:
Porolysis using heat source of electric arc dis...ge.
Top down gas flow structure…..minimizing powder build up.
Dual cooling jacket application….micorrosion inhibition system.
Plasma burner design provides a stable supply of plasma.
Simple structure for easy maintainability.
Features 20% lower water and power consumptions than burning type scrubber.
The Thunder is compatible with PFC gases such as SF6 that are difficult to abate with existing waste gas abatement systems. This state-of-the-art system minimizes running costs while maximizing abatement throughput.
Decomposes simultaneously.It is possible to handle PFC gas like SF6 and halogen like HBr simultaneously.
利用電漿來分解空氣污染物有下列優點:
1.去除效率高:較一般的焚化或觸媒反應法的反應性皆高,可使不易活化的反應快速進行。
2.節省能源:電漿在低氣體溫度即可產生,而電漿化學反應可以在近於室溫下進行,無須加熱氣體即可使反應完全,因此可節省能量甚巨。電漿可以將能量直接用在分子的鍵結破壞,而不需浪費能量來提高氣體的溫度。尤其是氣體的熱傳效率相當差,電漿在氣體低溫時即可破壞鍵結的能力,可大大的節省能源。
3.操作成本低廉且可避免二次污染:不需要吸收劑或吸附劑等化學藥品,也毋需觸媒或燃料,可同時節省操作費用,並避免二次污染。
4.設備體積小:電漿反應器較吸收塔、吸附塔或焚化爐小,不佔空間,非常適合既有工廠空氣污染之改善。
5.可處理低濃度污染氣體:能夠處理濃度範圍為ppb 至ppm 之惡臭和有害氣體。
6.由於世界各國對PFCs氣體的重視,處理PFCs氣體的設備,從燃燒方式、觸媒方式到目前的電漿方式…等,主要就是要降低PFCs氣體對全球溫室效應的影響。
7.電漿火炬為熱電漿源的一種,其中心高達10000℃以上的極高溫度,可用來處理科技產業所製造出來的廢氣。
8.電漿處理方式,對PFCs氣體的處理效率>95%以上,且可以處理任何廢氣,將是未來廢氣處理機台的主要方式之一。
9.本系統為熱電漿污染減量程序(Thermal Plasma Abatement Process)的應用。熱電漿污染減量程序可用來破壞任何液態或氣態之有機廢棄物,尤其適用於破壞高濃度的鹵化有機廢棄物,以下為幾項應用:
A.去除特殊廢棄物,像是會破壞大氣臭氧層的物質,例如海龍(滅火用化合物)、全氟碳化物(PFCs)、氟氯碳化物(CFCs)。
B.破壞任何蒙特婁議定書附錄A、B、C中所列出之管制物質。
C.對於難去除的有機污染物(POPS):戴奧辛、阿特靈、可氯丹、滴滴梯、六氯苯、多氯聯苯…等之處理,可作為焚化之替代程序,效果佳且節省成本。
D.可做為線上廢棄物管理(潔淨生產)的部分組成,應用於化學及製藥工業。
E.做為可移動之污染去除系統,適合用於現地復育及小規模之應用。
10.熱電漿技術應用於污染減量的優點:
A.製程中或積聚之有害廢棄物的最終去除。
B.高廢氣處理性能,實現大容量處理,處理流量MAX 1000LPM,不同製程處理量不同.
C.應用於製程中極有可能有助於大幅提升產能及產品品質;例如,目前已可引進改良製程,以減少有害副產物的產生。
D減少SiO2等粉塵閉塞,排放,穩定運行.
E急速升降溫,開關機耗時短.
F待機時進入OFF狀態,高效節能節電.
G.提供極為安全的操作程序。整個程序完全由電腦控制及監測,同時在任一時段內,只有少量體積的廢氣被處理。
H停電時自行啟動安全互鎖,更大程度保護設備.
I.無毒性殘餘物產生。
J.排放至大氣的污染濃度顯著低於現存以及建議之國際標準。國際毒性當量(戴奧辛)排放(I-TEQ)<0.1 ng/m3。
K.無有害蒸氣排放。
L.處理過程無異味產生。
M設備整體相對小型精巧,內部構造簡單,便於維護.
N.和成效相當的其他污染減量技術相比,投資成本較低。
O.維修簡易、乾淨且不昂貴。
P低運行成本,低維護費.
Q.可先行訓練程序操作人員